Moblie: 8613816755915
What is a Prefabricated Modular Home
Prefabricated modular home are the ultimate prefabricated building system. These highly customizable, environmentally-friendly homes are built almost entirely in a factory setting, saving both home owners and builders time, effort and money.
Once the main modules of the new house have been built – including the connected walls, floors, ceilings, wires, pipes and indoor fixtures – they will be transported to the plot selected by the owner, which can be manually placed on a permanent foundation by a crane or installed differently according to different forms of modules. Each house was designed and built in accordance with all state and national building and fire codes, and was ultimately completed by local builders.
Environmentally friendly
The essence of Prefabricated modular houses is green. Select environment-friendly building materials or recycled materials for secondary use to enable them to achieve the key components of green building certification. Modularization means that material waste is reduced in both the factory and the construction site, while simple assembly in the construction site reduces construction pollution caused by on-site construction. As a result, the environmental impact on the communities where land and housing are delivered has been mitigated. Modular houses are usually built more compactly and therefore more energy-efficient, which can reduce heating and cooling costs for owners.
Flexible modular home design
Although most manufacturers have a series of home plans to choose from, when planning a new Prefabricated modular home, computer aided design (CAD) allows unlimited design and customization possibilities, which can better reflect the owner’s personality. The modular structure allows rapid transition between ground breaking and occupancy. The design can be changed according to the owners’ ideas at different times. Typical modular houses can be moved in in about three months, or even less. Generally, the finished products are more novel and humanized than the houses built on site.
Save money and time
The design and construction meet or exceed the local building codes, and allow nearly 90% of the houses to be built outside the site. A highly customizable house can be built in a controlled factory environment. At the same time, the construction site is also in preparation, and the construction site only requires simple assembly. This saves the time of the owner and the construction party to a certain extent.
Most of the work is completed in the factory, so weather delay, material loss and subcontractor’s non appearance are almost eliminated. Since most of the design and construction are completed before installation, waste and communication costs are eliminated and money is saved. Building prefabricated modular houses can save time and money, so that builders can focus on product design and meet the needs of different customers.
Quality Construction
Prefabricated modular home in a factory setting allows for more consistent quality due to uniform construction processes, training techniques and inspections. All homes are inspected by an independent, third-party home inspection agency before leaving the factory. Once on site, they are again inspected, this time by a local building inspector. These homes meet and often exceed all requirements of locally adopted building and fire codes.
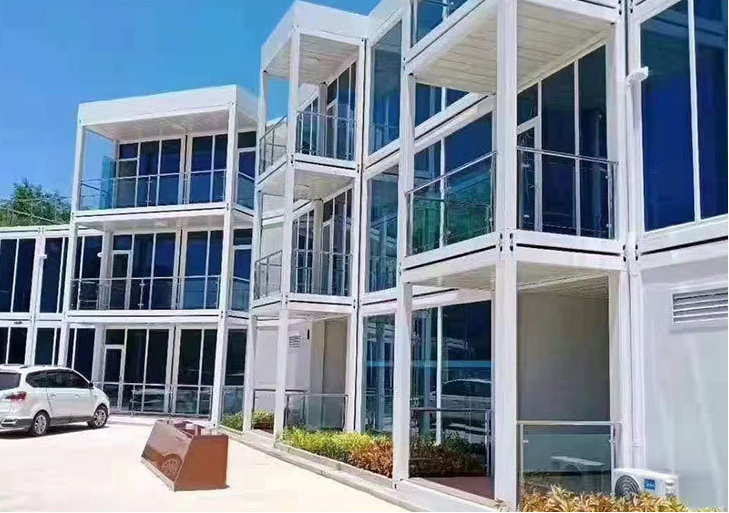